Establishing a wood pellet production plant requires careful selection of machine components to ensure efficient operation, consistent pellet quality, and optimal performance. The choice of components significantly depends on the type of raw materials being processed. This article offers guidance on selecting the appropriate components for wood pellet making machines tailored to different materials.
Flat Die vs. Ring Die Pellet Mills
The initial decision involves choosing between a flat die and a ring die pellet mill, with considerations for production scale, raw material type, and budget.
- Flat Die Pellet Mills: Ideal for small to medium-scale production, flat die mills can handle a range of raw materials, including wood, agricultural residues, and grasses. These machines are generally more affordable and easier to maintain due to their simpler design, although they tend to have lower production capacities compared to their ring die counterparts.
- Ring Die Pellet Mills: Designed for large-scale production, ring die mills excel at processing wood-based materials. They provide higher throughput and produce more uniform pellets. However, these machines feature a more complex design and come at a higher cost than flat die models.
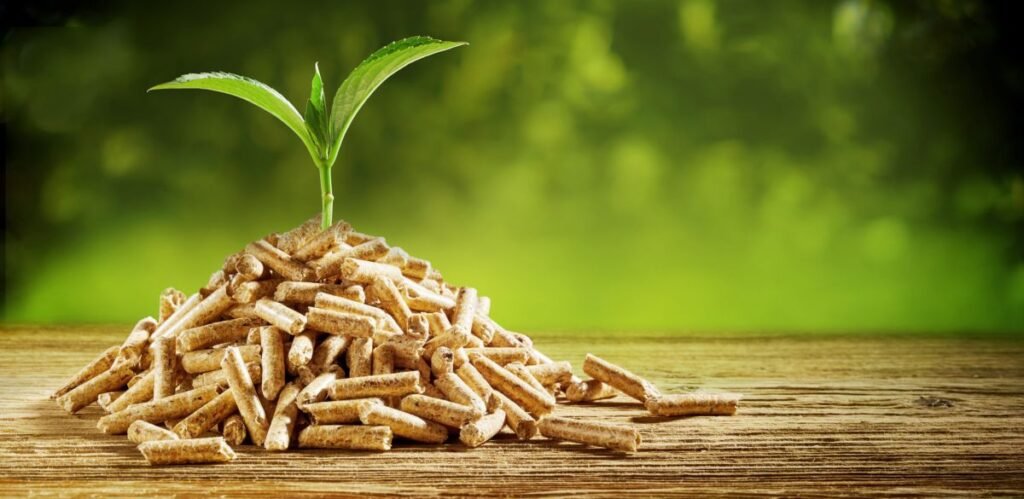
Choosing the Right Die Material
The die is a critical component in any pellet mill, directly influencing pellet quality and durability. The selection of die material should be based on the abrasiveness and density of the raw materials being processed.
- Wood-based Materials: Stainless steel dies are recommended for wood chips, sawdust, and other wood-derived materials due to their excellent wear and corrosion resistance. Common materials for wood pellet dies include 4Cr13 or X46Cr13.
- Agricultural Residues: Materials like straw, corn stover, and rice husks are generally more abrasive than wood. For these, alloy steel dies, such as 40Cr or 35CrMo, are preferred, as they undergo heat treatment to achieve a hardness of 50 HRC or higher, providing excellent durability.
- Grasses and Herbaceous Materials: Due to their high silica content and fibrous nature, grasses can be challenging to process. Dies made from tungsten carbide or ceramic composites are ideal, offering superior wear resistance to withstand the abrasiveness of these materials.
Roller Design and Material Selection
Rollers play a crucial role in determining pellet quality and machine performance. The design and material of the rollers should align with the raw materials being processed.
- Wood-based Materials: Rollers made from alloy steel, such as 40Cr or 42CrMo, are commonly used in wood pellet production. These steels are heat-treated to achieve a hardness of 45-50 HRC, striking a balance between wear resistance and toughness. A tapered roller design ensures even wear and prevents slippage.
- Agricultural Residues: For agricultural residues, harder surface rollers are recommended. Rollers made from 60Mn or 60Si2Mn steel, with a hardness of 55-60 HRC, are capable of withstanding the abrasiveness of these materials. The roller surfaces can also be coated with tungsten carbide or ceramic for enhanced wear resistance.
- Grasses and Herbaceous Materials: Rollers with serrated or grooved surfaces can grip fibrous materials effectively, preventing slippage. Tungsten carbide or ceramic coatings further improve wear resistance.
Gearbox and Bearing Considerations
The gearbox and bearings are essential for transmitting power and minimizing friction in the pellet mill. Selection should take into account production capacity, raw material type, and operating conditions.
- High-capacity Production: For high-capacity pellet mills, planetary or helical-bevel gearboxes are preferred due to their efficiency and load-bearing capabilities. Bearings should be chosen based on expected loads and speeds, with high-quality options from reputable manufacturers recommended.
- Abrasive Materials: When processing abrasive materials like agricultural residues or grasses, protecting the gearbox and bearings from wear and contamination is vital. Sealed bearings and gearboxes with enhanced sealing systems can prevent abrasive particles from entering and prolong component life.
- Harsh Environments: In environments with extreme temperatures or humidity, specialized gearboxes and bearings designed for these conditions should be employed to ensure reliable operation and prevent premature failure.
Maintenance and Wear Parts Management
Regular maintenance and timely replacement of wear parts are crucial for maintaining the long-term performance and efficiency of wood pellet making machines. Consider the following when selecting machine components:
- Wear Parts: Identify components most prone to wear, such as dies, rollers, knives, and screens. Ensure that replacement parts are readily available from the manufacturer or authorized suppliers.
- Maintenance Requirements: Opt for components that are easy to access and maintain. Features like quick-release mechanisms for die and roller changes and easy-to-clean surfaces enhance maintenance efficiency.
- Lubrication: Select components that require minimal lubrication and feature extended lubrication intervals to help reduce maintenance costs and downtime.
Conclusion
Selecting the right components for wood pellet making machines based on raw materials requires careful consideration of production scale, material characteristics, and operating conditions. By choosing the appropriate die material, roller design, gearbox, and bearings, you can optimize the performance and efficiency of your pellet production plant.
Additionally, regular maintenance and timely replacement of wear parts are essential for maintaining consistent pellet quality and maximizing the lifespan of your equipment. Collaborating with reputable machine manufacturers and adhering to their recommendations will ensure that your wood pellet making machine effectively addresses the specific challenges posed by your raw materials.