Establishing an organic fertilizer production line in Australia necessitates careful planning and investment in specialized equipment. With the Australian organic fertilizer market projected to reach USD 254.37 million by 2032, an efficient production line is crucial for success in this competitive industry. This article provides an overview of the key equipment needed for a comprehensive organic fertilizer production line tailored to the Australian context.
1. Raw Material Handling Equipment
Reception and Storage Units
- Storage Bins: Concrete or steel storage bins to accommodate various raw materials.
- Covered Storage Areas: Protect materials from weather conditions, particularly in regions with variable climates.
- Weighbridge: For accurate measurement of incoming materials, ensuring precise formulations.
Conveyor Systems
- Belt Conveyors: Efficiently transport raw materials between processing stages.
- Screw Conveyors: Ideal for moving powdery or granular materials with ease.
- Bucket Elevators: For vertical material transport, particularly useful in multi-level facilities.
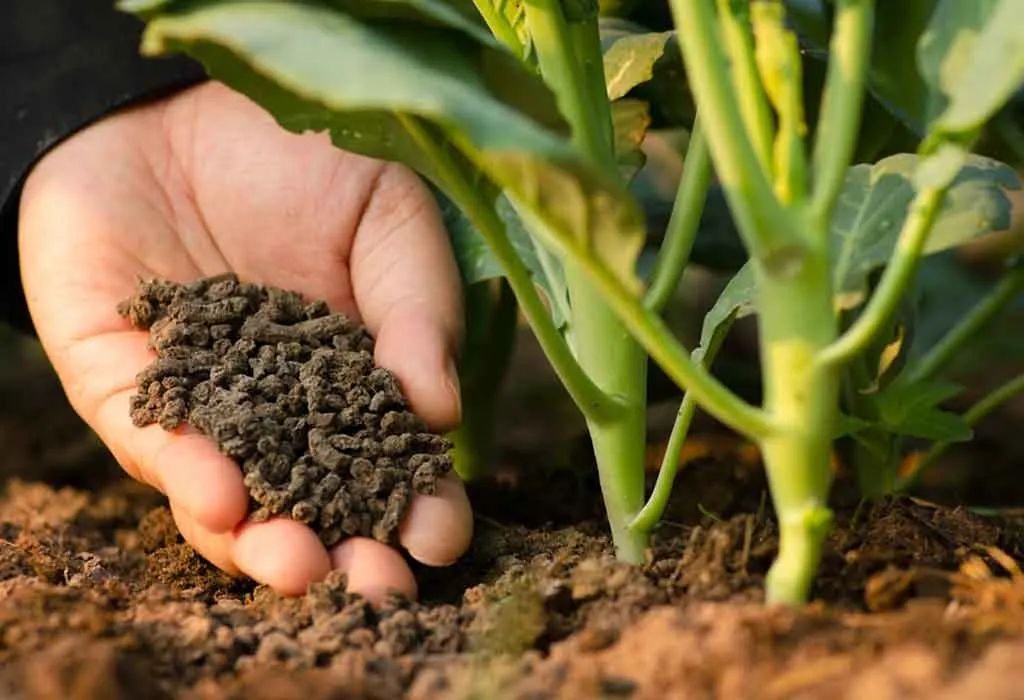
2. Pre-processing Equipment
Crushing and Grinding Machinery
- Hammer Mills: Break down larger organic materials, making them suitable for further processing.
- Grinders: Ensure uniform particle size, which is critical for consistent product quality.
- Pulverizers: Achieve fine grinding of mineral additives, enhancing nutrient availability.
Mixing Equipment
- Horizontal Paddle Mixers: Provide thorough blending of various ingredients.
- Vertical Screw Mixers: Ensure homogeneous mixing, crucial for consistent nutrient distribution.
- Ribbon Blenders: Suitable for handling larger volumes, particularly in high-capacity production lines.
Composting Equipment (if applicable)
- Windrow Turners: Self-propelled or tractor-pulled models for aerating compost piles, crucial for large-scale composting operations.
- In-vessel Composting Systems: Enclosed systems that accelerate composting with controlled temperature and moisture conditions.
- Aeration Systems: Blowers and piping for forced aeration, improving compost quality and reducing processing time.
3. Granulation Equipment
Disc Granulators
- Form spherical granules from powdered materials, ideal for producing uniform and marketable organic fertilizer pellets.
Drum Granulators
- Suitable for continuous granulation of organic materials, ensuring high production efficiency.
Extrusion Granulators
- Produce cylindrical granules, offering versatility in pellet shape and size.
4. Drying Equipment
Rotary Dryers
- Reduce moisture content in granulated fertilizer, ensuring product stability and shelf life.
Fluidized Bed Dryers
- Provide efficient drying with uniform heat distribution, particularly suitable for large-scale operations.
Belt Dryers
- Offer gentle drying for heat-sensitive organic materials, maintaining nutrient integrity.
5. Cooling Equipment
Rotary Coolers
- Reduce the temperature of dried granules, preventing clumping and ensuring safe packaging.
Fluid Bed Coolers
- Provide rapid and uniform cooling, enhancing product quality and storage stability.
6. Screening and Sorting Equipment
Vibrating Screens
- Separate granules by size, ensuring consistent product quality.
Air Classifiers
- Remove dust and fine particles, improving product purity.
Magnetic Separators
- Eliminate metallic contaminants, safeguarding product quality and equipment longevity.
7. Packaging Equipment
Weighing and Bagging Machines
- Accurately measure and package the final product, ensuring consistency and reducing waste.
Sealing Machines
- Securely close bags of fertilizer, protecting against moisture and contamination.
Palletizing Systems
- Stack and store packaged products efficiently, optimizing warehouse space.
8. Quality Control Equipment
Moisture Analyzers
- Monitor moisture content throughout the production process, ensuring optimal product conditions.
Nutrient Analysis Equipment
- Test N-P-K content and other essential nutrients, guaranteeing product compliance with market standards.
pH Meters
- Measure the acidity or alkalinity of the fertilizer, crucial for maintaining product stability.
9. Environmental Control Systems
Dust Collection Systems
- Maintain air quality and recover fine particles, contributing to a safer working environment.
Odor Control Units
- Manage odors using bio-filters or chemical scrubbers, essential for complying with environmental regulations.
Wastewater Treatment Systems
- Process and recycle water used in production, aligning with Australia’s water conservation efforts.
10. Automation and Control Systems
Programmable Logic Controllers (PLCs)
- Automate various stages of the production process, enhancing efficiency and consistency.
Supervisory Control and Data Acquisition (SCADA) Systems
- Monitor and control the entire production line, providing real-time data for informed decision-making.
Sensors and Monitoring Devices
- Track temperature, humidity, and other parameters in real-time, ensuring optimal production conditions.
Considerations for Equipment Selection
When choosing equipment for an organic fertilizer production line in Australia, several factors should be considered:
- Scale of Production: Select equipment that matches your production capacity and allows for future expansion.
- Raw Material Characteristics: Ensure the equipment is compatible with the specific types of organic materials you will be using.
- Energy Efficiency: Opt for energy-efficient equipment to reduce operational costs and consider integrating renewable energy sources.
- Water Conservation: Choose equipment that minimizes water usage, important for aligning with Australia’s environmental policies.
- Compliance with Australian Standards: Ensure all equipment meets safety and environmental standards, and consider certifications like CE marking.
- Adaptability to Climate Conditions: Choose equipment that can withstand Australia’s diverse climate conditions, such as corrosion-resistant materials for coastal areas.
- Local Support and Maintenance: Prioritize equipment with readily available spare parts and local technical support.
- Integration Capabilities: Ensure compatibility with existing systems, particularly if you are expanding an existing facility.
Innovative Technologies to Consider
- IoT-enabled Equipment: For real-time monitoring and predictive maintenance, enhancing operational efficiency.
- AI-powered Quality Control Systems: Advanced systems for ensuring consistent product quality.
- Precision Dosing Systems: Accurate blending of micro-nutrients, critical for high-quality organic fertilizers.
- Biochar Production Units: Incorporate biochar into organic fertilizers to improve soil health and product value.
Conclusion
Establishing an organic fertilizer production line in Australia requires a significant investment in specialized equipment that ensures efficiency, quality, and compliance with local standards. As the demand for organic fertilizers grows, driven by consumer preferences and government support for sustainable agriculture, a well-equipped production line will be essential for success.
By selecting the right equipment and staying abreast of technological innovations, businesses can establish a state-of-the-art production line that meets the evolving needs of Australia’s agricultural sector. This approach not only positions a company for profitability but also contributes to the broader goal of promoting sustainable agricultural practices in Australia.